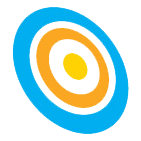
Website Asset Recruitment
Asset Recruitment
ref 01122
Chemical Process Engineer (General)
Duration: 12 Months contract
ROLE
Reporting to Manufacturing Lead/Manufacturing Technology Lead, Process Engineer will support activities of Manufacturing Technology team with responsibility for providing engineering support to ongoing requirements for Manufacturing 7 as well as supporting any future tech transfer projects into MFG7.
RESPONSIBILITIES
• Assist in site start up and project related activities (particularly CQV):
o Support package owners on vendor management and equipment or process related activities and queries.
o Generate equipment verification & validation protocols and reports as required.
o Review vendor documentation for completeness and accuracy.
o Participate in FAT and vendor related activities.
o Participate in commissioning of process equipment and associated automation as needed. Support issue resolution in se areas as needed.
o Support CQV execution team by participating in verification & validation related activities as required.
• Ensure equipment is designed and tested to meet requirements of process, to ensure that equipment continues to run as intended, that it is appropriately validated and maintained in that validated state.
• Coordinate delivery of a robust process and reliable equipment in support of a Right First Time Operating Unit.
• Support implementation of Global Requirement Program tools and techniques within Operation Unit. (for e.g. Operator Care, PdM, PMO, Work Management)
• Participate in and/or lead facility fit assessments for new product introductions.
• Implement equipment CAPA’s and performance improvements
• Provide equipment technical support and troubleshooting.
• Provide routine Automation support, troubleshooting and maintenance.
• Support use of PI to provide business efficiency.
• Identify equipment and process improvement projects as needed.
• Work with portfolio management process to identify projects/support demands from Core Units.
• Champion and Support Energy saving programs/projects within Operating Unit.
• Write equipment assessments to support investigation closure.
• Change Control write up and close out.
• Ensure investigations are closed on time, recurring deviations are tracked, and that true root cause and effective CAPA are identified and implemented.
• Participate in cross-functional project teams as applicable
• Support audit preparation.
• Implement and support continuous improvements that reduce cycle times and operational costs.
• Develop and maintain database for department tracking and data analysis needs, as applicable
• Complete biennial review and PQS updates.
• Support disposition process. Ensure all data ready in timely fashion in support of OpU disposition metric.
• Perform additional duties at request of direct manager.
• Perform all duties in accordance with GMP requirements, SOPs and controlled documents.
• Will be flexible to take on additional tasks and responsibilities at discretion of Manufacturing Lead/Manufacturing Technology Lead.
• Will act as a role model for Manufacturing function and also wider organisation in adherence to client corporate core values and PROUD culture.
PERSON SPECIFICATION
Technical Competencies
• Excellent communication skills including computer literacy and ability to work independently and in team
• Experience and knowledge of DeltaV (or equivalent) MCS platform preferred.
• Familiarity with Bioreactor, Chromatography and Ultra filtration production operations is desirable.
Experience
• Minimum of 5 years’ experience in a large-scale in a Biopharmaceutical/pharmaceutical facility.
• Ideally, experience working in a Manufacturing Technology team in a ‘greenfield’ context of similar size and scale.
• Ideally, experience using DeltaV (or equivalent) MCS platform in a commissioning or process development environment.
Knowledge
• Thorough knowledge of current Good Manufacturing Practices (cGMP).
QUALIFICATIONS
• Third level qualification in a Science or Engineering related subject is preferable.
Behavioral Competencies
• Excellent interpersonal, verbal, and written communication skills
• Able to think critically and demonstrate troubleshooting and problem solving skills
• Self-starter and self-motivated; organized with good attention to detail
• Comfortable working in a fast-paced environment and able to adjust workloads based on changing priorities
• Collaborative and inclusive approach to work and colleagues.
• Engage cross functionally in conjunction with a site-based team.
• Demonstrate strong ethics in adhering to company procedures and policies, regulatory standards, and our customers’ expectations
ONEROUS REQUIREMENTS
• Must be willing to travel as required internationally to fulfil responsibilities of position.